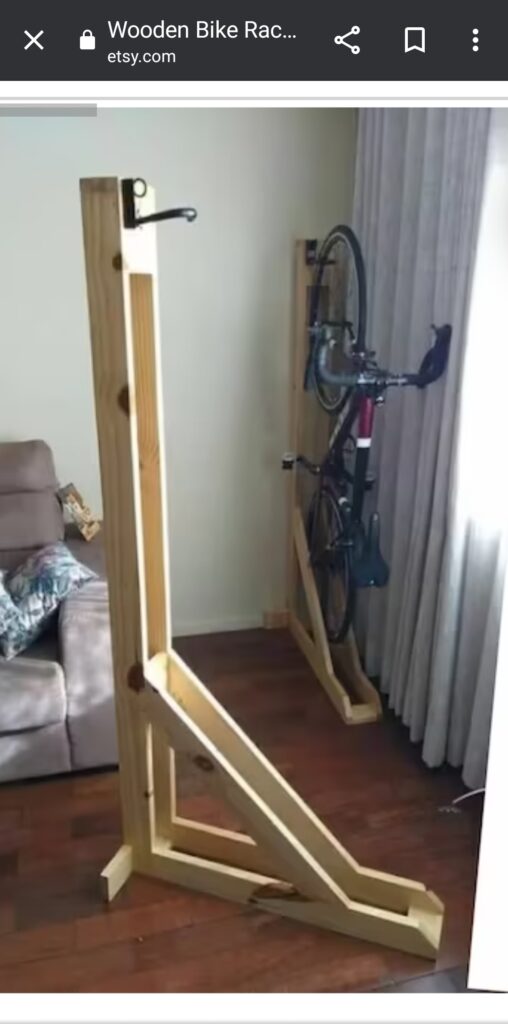
T-shirts >
video1
video2
video3
video4
video5
video6
Screen printing info >
- I think I wrote it down but what mesh is the screen I have and what are popular mesh sizes
- After I build frame with hinges, practice pressing ink on paper
- I need to make trailer image a little bigger
- Since screens are easy to make, the best thing to do is reuse screen and store transparencies – maybe get a couple of different screens
- Do a white trailer design on green in blue shirts and blue surfer design on white shirt
- How to make frame with hinges so when lifting screen the image placement is always the same on the fabric
- How many passes with the ink?
Steps for creating design >
- Make my image as black as possible when printing so I don’t have to go over it with a sharpie
- Figure out setting on printer for transparency
- Transparencies – it says on package what side to use, but you can test with a sharpie, make a little mark, it feels different (you can also test with Windex since it messes up the printing side, test in small area in corner
- Put printing side down in printer
Steps for creating screen and applying ink >
- Apply emulsion, it only takes a very small amount, coat both sides of screen and remove any excess
- Put screen in darkness overnight (I put it under workbench with a cover over the top of it)
- Use very little light, just enough to see, when spreading emulsion – then, use nothing but exposure light when exposing emulsion for design (use a timer for 7-8min when using my 10×14 screen and have the light about 16in away from screen)
- Attach transparency image and place light source 16in from frame and expose for 7-8min making sure light hits entire screen
- Wash out screen to expose image, no hot water, use a tooth brush if needed
- Clean off design right after exposure so it doesn’t set too much, making it hard to clean
- Get shirt for print and run color through screen for print, tape coins under frame by image to lift slightly off fabric for better print quality
- If absolutely necessary, fix screen print designs with a small brush, dilute ink slightly – if brush is “hairy”, get it back to a sharp tip for fine line painting and touch-up by dipping in hot water and shaping with fingers
- Heat setting is the final step in the screen printing process. Let the ink dry completely. You can speed up the drying process by using a fan or placing the fabric in a well-ventilated area. Use a heat press or iron to apply heat to the fabric. The temperature should be the highest the fabric can withstand without scorching. Press the fabric for at least 40 seconds using a heat press set to 320° F. You can also use an iron on the setting recommended for your fabric type. Move the iron continuously over the design for 2–3 minutes. Heat setting bonds the ink to the fabric so it won’t fade in the wash. If you skip heat setting, the design may fade over time